Material Temperature Sensitivity
I wrote a finite difference (FD) thermal field solver from scratch in C++, with a forward Euler (explicit) time integration scheme. The thermal FD solver was formulated for both a lumped-mass model and for a 3D domain. Both models were applied to a selective laser sintering (SLS) process, which is an additive manufacturing technique where a laser scans and melts the top surface of a powder bed, sequentially building components layer-by-layer.
Additionally, I built a wrapper that ran multiple deterministic simulations for quantifying the sensitivity of the thermal field based on slight input paramenter changes. In this case, the laser power input setting was perturbed.
BASF SE provided the financial support for this study. Their material research division employed my thermal FD solver as a tool to aid their scientists develop the Ultrasint® PA6 product line for SLS processing.
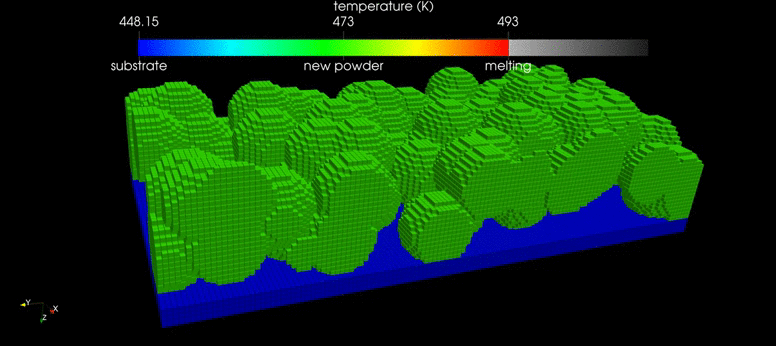
Here, we see a voxelized representation of a randomly deposited powder bed. Each spherical particle is discretized into a collection of voxels. Above, a cross section of colored voxels representing local material temperatures and phases. Below, a perspective view of the material particles, showing evidence of irradiation by a static, overhead Gaussian laser beam.
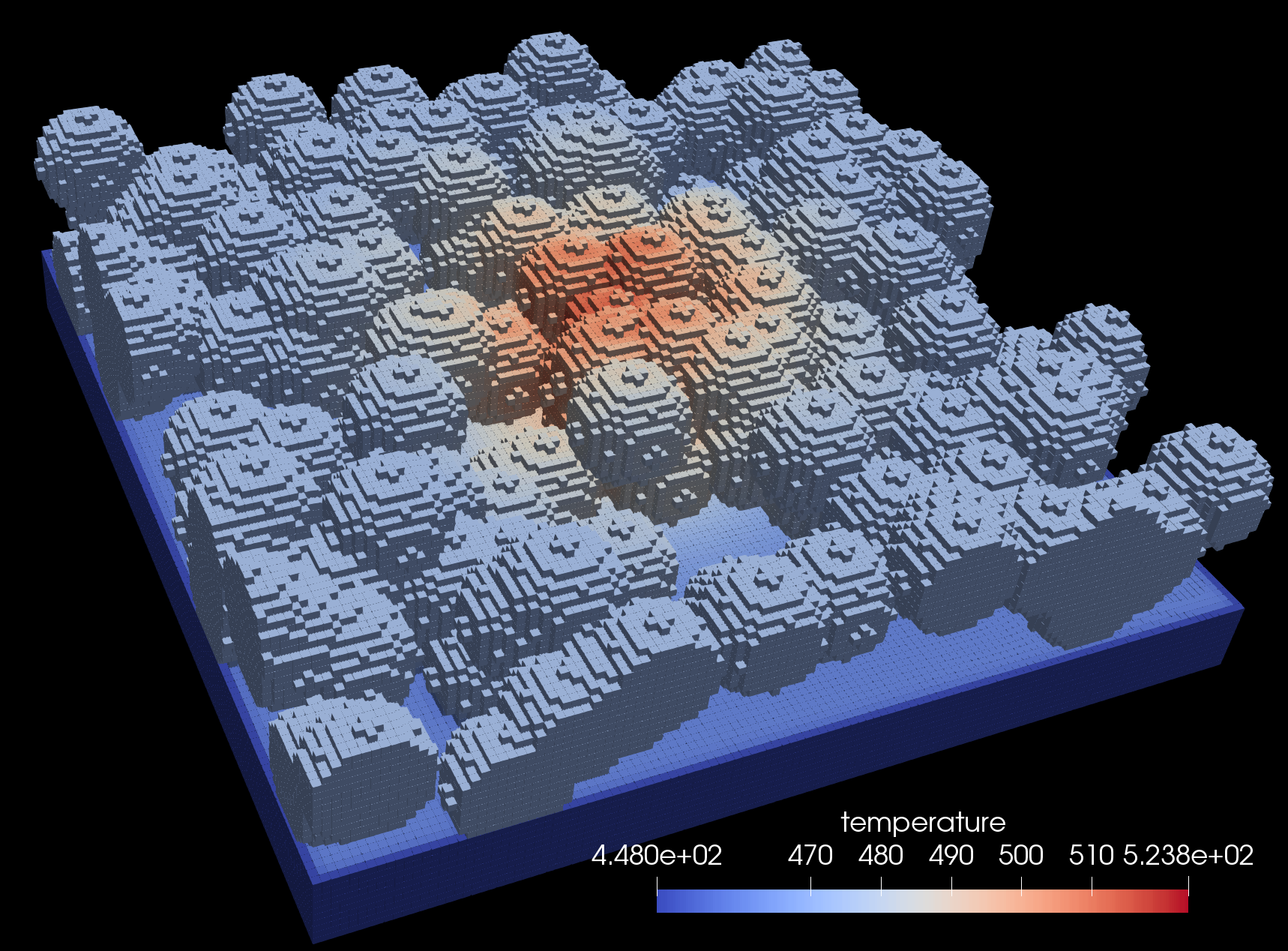
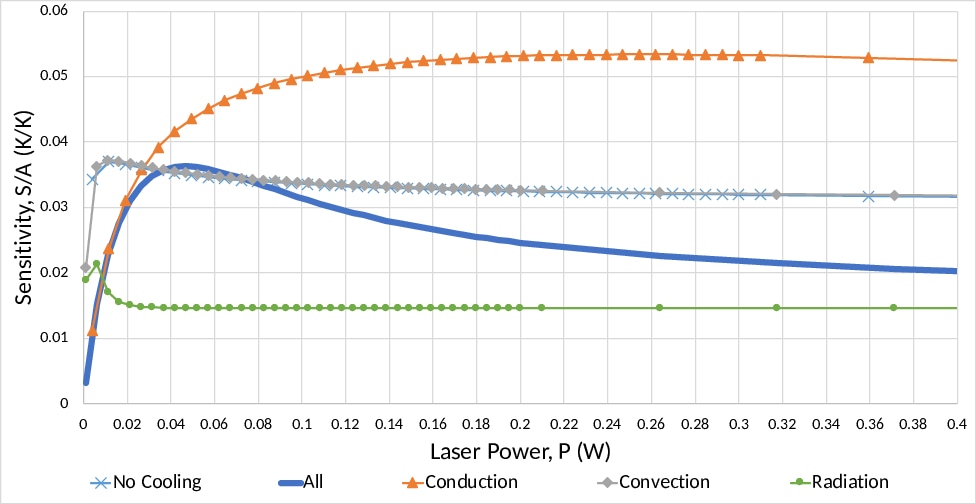
Above is the sensitivity of final material temperatures of a lumped-mass model (single particle) for different thermal model cases. (X) Without any thermal contributions – no cooling, (–) with all thermal contributions, and (▴)-(●) with isolated thermal contributions.
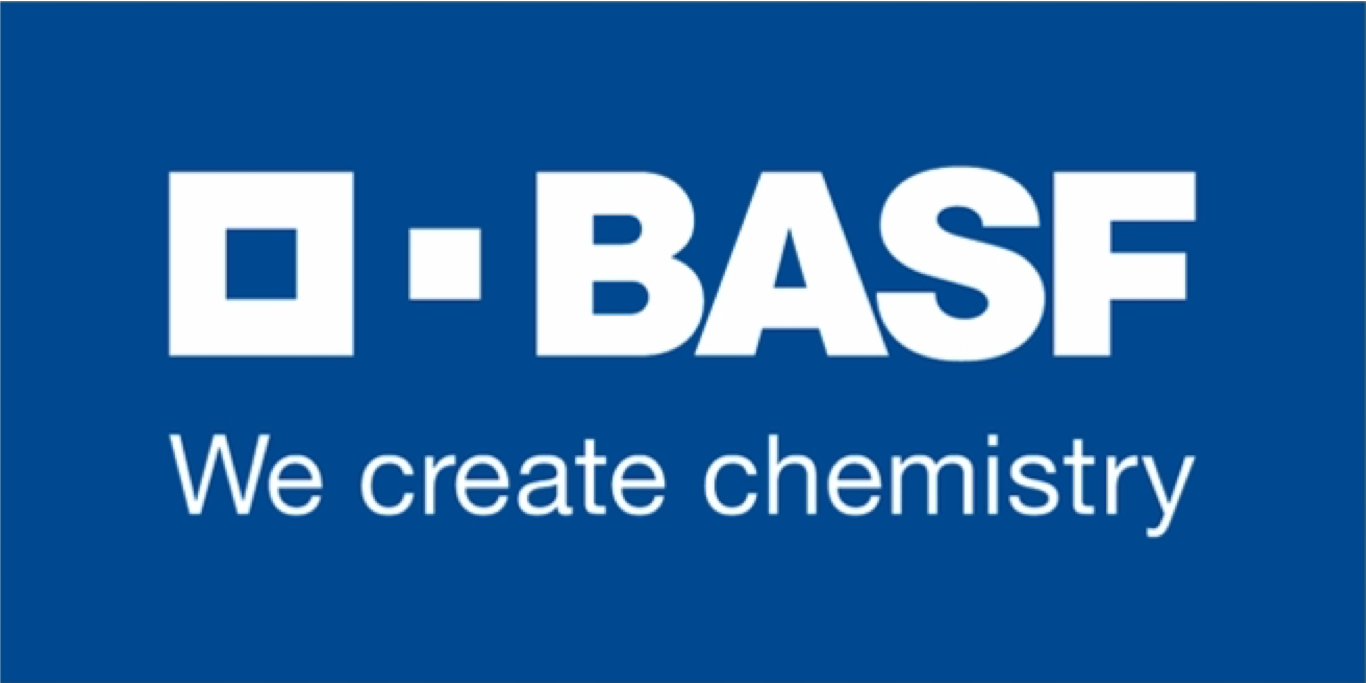