Uncertainty in Manufacturing
I built a physics-based simulation of the selective laser sintering process (SLS) in Python, without third party software. This simulation solves the energy balance PDE to solve for the temperature field of an SLS domain. I use the temperature data to build a reduced order model to reduce runtime and to quantify the uncertainties of the SLS process.
The Problem: In this study, I use the paper by Ganeriwala & Zohdi to recreate true SLS conditions. In this sample problem, a set of discrete powder particles is deposited stochastically over a previously solidified substrate. Then, a laser scans directly overhead in a single track, heating up and melting the powder and the substrate. I solve the heat equation via a coupled discrete element-finite difference method in 3D to evolve particle and substrate temperatures.
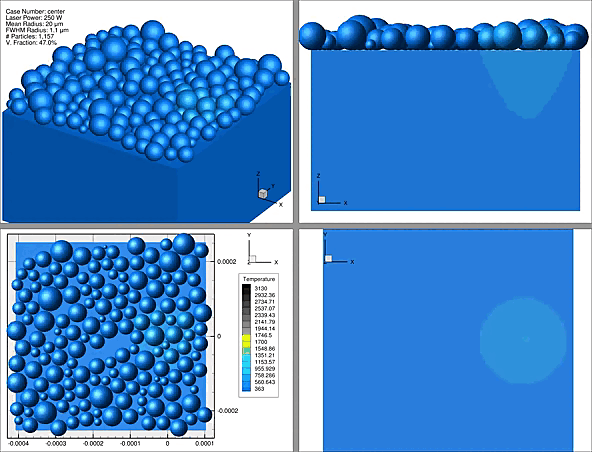
Uncertainty Quantification: I have injected a random effect into the model to simulate an aleatoric source of uncertainty. This random effect is executed with a particle generator that uses a constructive front approach, an algorithm that adds a single particle at a time with a radius sampled from a predetermined Gaussian distribution. The local arrangement of the particles and the size of the particles will determine the local powder depth, which in turn determines the local amount of laser energy that penetrated through the powder layer down to the substrate. Since the simulation is stochastic, then the thermal field will vary every time it is run with the same input parameters.
Reduced Order Modeling: I use a snapshot proper orthogonal decomposition (sPOD) approach to approximate the temperature data across a parameter space. In this process, I have a 4x4x4 parameter space which varies the laser power setting and the generated particle size distribution parameters: the mean and the standard deviation. The temperature data for all 64 cases are stacked together onto a data array and using eigenvalue decomposition it is projected onto a reduced number of dimensions. My reduced model achieves about 150 dimensions, a reduction from about 590,000 degrees of freedom, to achieve a 2% maximum error when reconstructing the noisy temperature data.